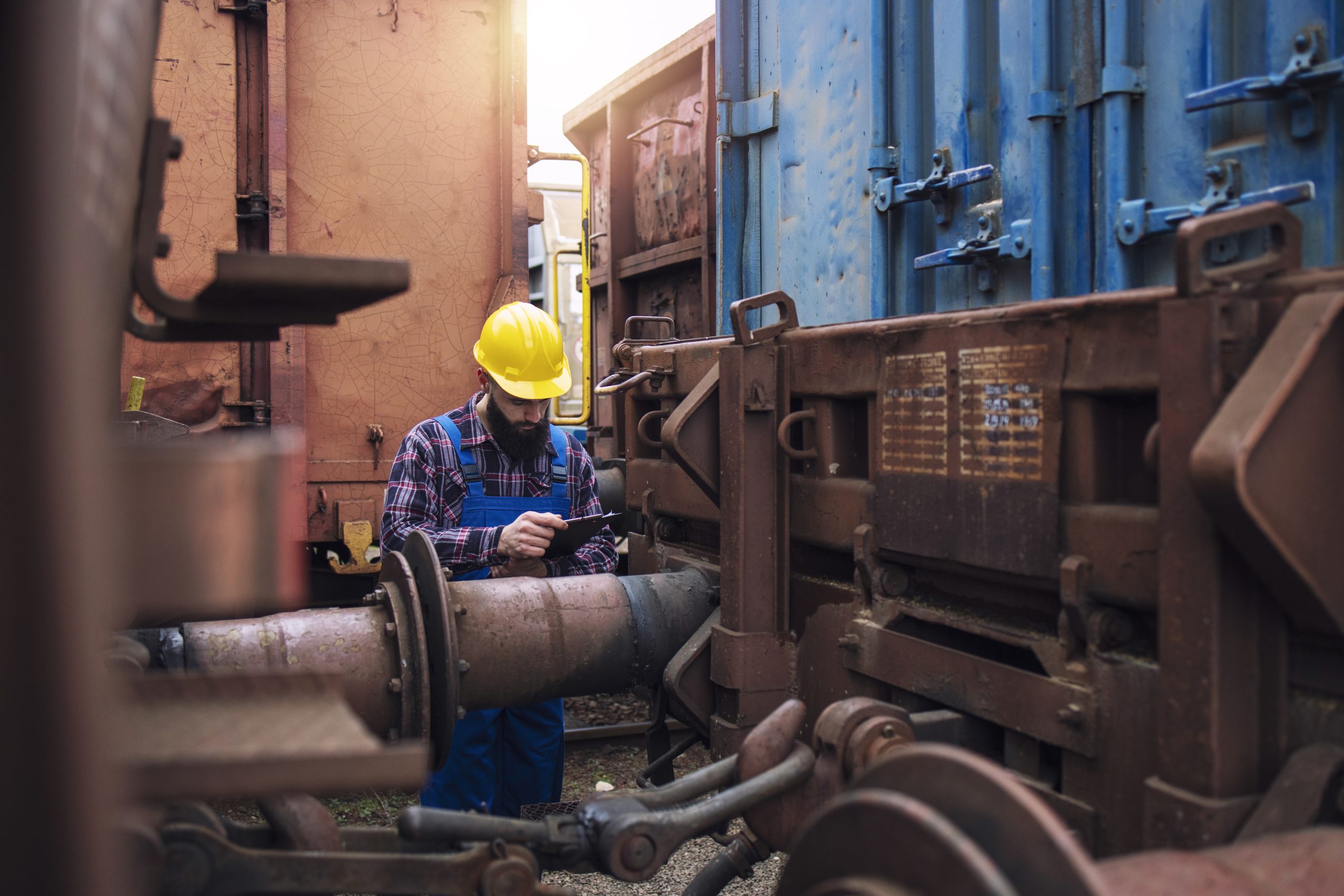
Una de las grandes aplicaciones del conjunto válvula-actuador, es el sector de transporte por ducto de hidrocarburos, un medio seguro que evita exponer a viajeros por los caminos y puentes del territorio nacional a incidentes que involucran hidrocarburos y sus riesgos correspondientes. Sin embargo, el transporte por ducto requiere superar retos para crear instalaciones seguras, algunos de estos retos son:
- La detección de fugas.
- Detección de tomas clandestinas.
- Detección de pequeñas y graduales fugas
- Corrosión y ruptura de ductos.
Principales causas de incidentes en el transporte por ductos.
En todos los aspectos mencionados anteriormente, el conjunto válvula-actuador forma parte importante de sistemas (sistemas de paro por emergencia) dirigidos a prevenir incidentes y en su caso reducir los efectos de una catástrofe.
Estos sistemas se forman por un lazo de control conformado por:
- Sensor y transmisor de presión. (Sensor-Elemento primario de control, Transmisor-Elemento secundario de control).
- Sensor y transmisor de temperatura. (Sensor-Elemento primario de control, Transmisor-Elemento secundario de control).
- Un controlador lógico.
- Un conjunto válvula – actuador. (Elemento final de control).
El funcionamiento básico de estos lazos de control inicia a partir del monitorear condiciones normales de las variables (presión, temperatura, etc) de operación del ducto, cuando se presenta una anormalidad en dichas variables o un cambio brusco, el sistema envía señal de cierre al actuador, el cual desarrolla un cierre rápido de la válvula como una de las fases de contención para detener el flujo de hidrocarburo a través del ducto.
Instrumentación para detección de fugas y sistema de paro por emergencia.
El riesgo que involucra la manipulación de los hidrocarburos, ha hecho necesario definir un nivel de confiabilidad de los sistemas de paro por emergencia, esta característica es una de las importantes diferencias entre un lazo de monitoreo y control de proceso, y un sistema de paro por emergencia.
Los sistemas de paro por emergencia cuentan con SIL “Safety Integraty Level”, una herramienta utilizada para definir la confiabilidad del diseño de una Función Instrumentada de Seguridad (FIS) o lazo de control (combinación de sensores, controlador y elementos finales de control) del sistema de paro por emergencia.
La diferencia entre un lazo de control de proceso y una función instrumentada de seguridad (FIS), es que, la función instrumentada de seguridad detecta un peligro o condición riesgosa del proceso y reacciona llevando el proceso a un estado seguro, como es el caso del actuador al detectar un evento no deseado como detección de fuga o ruptura de un ducto.
Existe una idea errónea, en la que se piensa que al integrar un FIS con elementos (sensores, controladores y actuadores) certificados con cierto nivel integral de seguridad (SIL), el sistema será altamente seguro. Con el presente artículo esperamos ampliar la visión del SIL y corregir algunas ideas equivocadas.
Como se puede observar en la siguiente tabla, el nivel más alto del SIL es el más confiable.
Niveles integrales de seguridad.
De la tabla se puede observar que el SIL define un rango de confiabilidad (90-99% de confiabilidad, 99-99.9% de confiabilidad, etc) y este rango de confiabilidad puede expresarse como probabilidad de falla en demanda (PFD) (0.1-0.01 probabilidad de falla, 0.01-0.00001 probabilidad de falla, etc.) o como factor de reducción del riego (RRF) (RRF= 1/PFD) (reducción de riesgo de 10-100 veces, reducción del riego de 100-1000 veces, etc.).
Todo mundo desea más confiabilidad en sus sistemas, sin embrago, la confiablidad de una FIS no se logra simplemente seleccionando el SIL deseado y asegurando que los componentes cuenten con el certificado del nivel SIL deseado, de igual manera un SIL no se homologa a toda una planta o instalación. El SIL está siempre asociado a una función instrumentada de seguridad (FIS) y si partimos de que un sistema instrumentado de seguridad (SIS), está compuesto por diferentes FIS, podremos comprender que, en un SIS, existirán tantos SIL’s como FIS existan.
El SIL es posterior a un análisis de riesgo HAZOP o LOPA, para identificación, evaluación y reacción a los riegos, sobre este último paso de reducción de riegos, el dueño del proceso define cuál es el nivel de riego que puede tolerar la planta.
Existen estándares para la definición de los procesos de análisis de riegos y todo el proceso descrito en el párrafo anterior y están amparados por la IEC (International Electrotechnical Commission). El estándar IEC-61508 dirigido a fabricantes de dispositivos, para diseñar componentes de alta integridad para ser utilizadas en una función instrumentada de seguridad, como involucrar nivel de diagnóstico de circuitos del dispositivo, software de auto pruebas, etc. Y el estándar IEC-61511 dirigida a diseñadores de proceso y operadores para implementar una función instrumentada de seguridad y alcanzar un factor de reducción del riego como redundancia de equipos, requerimientos adicionales e intervalos de pruebas.
Los estándares mencionados, ayudan -por mencionar algunos puntos- a realizar decisiones como:
- Tipo de dispositivos a utilizar en la función instrumentada de seguridad (sensores, controladores y elementos finales de control).
- Arquitectura de los componentes, que define nivel de redundancia.
- Lógica de operación, que determina como una acción inicia basada en señales en conflicto.
- Intervalo de pruebas, cómo y cuando cada componente debe ser probada.
Una vez decidida a través del análisis LOPA ó HAZOP el SIL requerido, el estudio y consolidación del SIL se desarrolla a partir de cinco pasos principales.
Paso 1: Descomponer el FIS en componentes y arquitectura, por ejemplo, la función de paro por emergencia de ducto mencionada anteriormente, podría ser de la siguiente manera:
Componentes de Sistema Integral de Seguridad de un paro por emergencia.
Paso 2: Calcular la probabilidad de falla en demanda (PFD) de cada componente, un ejemplo de las fórmulas posibles de uso es:
Donde se está considerando:
ƛDU= Tasa de falla peligrosa no detectada.
T1= Intervalo de aplicación de pruebas.
MRT= Tiempo promedio de reparaciones.
ƛDD= Tasa de falla peligrosa detectada.
Nota: La fórmula es para fines de ejemplificación, las fírmulas pueden cambiar en tre otros factores, por tratarse de una estructura simple, dobre redundancia, triple redundancia, etc.
Paso 3: Determinal la probabilidad de falla en demanda del FIS como un todo, esto es simplemente la suma de cada componente. Nota: esto aplica solomante si no existiera redundancia.
Paso4: Convertir la probabilidad de falla en demanda (PFD) del FIS a factoro de reducción de riesgo (RRF) “1/PFD”.
Paso 5: Comparar si el valor obtenido cumple con el SIL requerido de acuerdo al estudio LOPA o HAZOP. De presentarse el caso, que el FIS no cumple con el SiL necesario, se consideraran otras actividades como:
- Analizar el SIL del elemento del FIS con mayor probabilidad de falla.
- Aplicar alguna topología en redundancia.
- Aumentar frecuencia de pruebas del equipo.
Cabe mencionar, como se observa en la fórmula, un SIL mayor frecuencia de pruebas y horas de mantenimiento de los componentes, tareas que de no cumplirse impiden mantener el nivel de seguridad para el cual fue diseñado el sistema.
Como conclusión:
Los procesos que involucran manipulación de hidrocarburos, requieren de sistemas adicionales a los tradicionales sistemas de monitoreo y control de procesos, llamadas funciones integrales de seguridad que involucran los sistemas de paro por emergencia.
El SIL define un grado de confiabilidad de las funciones instrumentadas de seguridad.
El SIL no es olo un certificado, detrás de un SIL existe una metodología para detarminar el mejor método de funcioanmiento de un FIS adecuado a un proceso.
Entre mayor es el SIL de un FIS mayor es la frecuencia de pruebas y horas de mantenimiento de los componentes, tareas que de no cumplirse impiden mantener el nivel de seguridad para el cual fue diseñado el sistema.